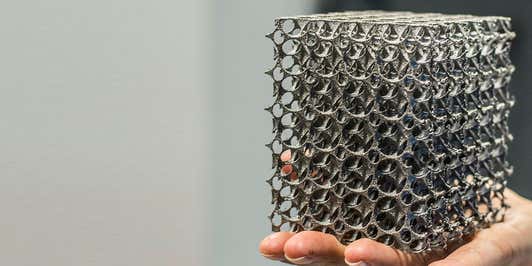
금속 분말 또는 분말 금속은 코팅, 안료, 불꽃놀이, 배터리 등 다양한 응용 분야에 사용됩니다. 금속 분말의 가장 크고 빠르게 성장하는 응용 분야는 분말 야금 및 적층 제조 분야로, 최소한의 마감으로 최종 크기와 모양에 가까운 부품을 생산할 수 있는 정밀 형상 제조 기술에 가깝습니다.
압축 및 소결과 같은 기존의 분말 야금 공정은 1920년대부터 금속 성분을 생산하는 데 사용되었고, 열간 등압 성형(HIP) 및 금속 사출 성형(MIM)과 같은 공정은 각각 1960년대와 70년대 이후에 사용되었습니다. 적층 제조는 레이저, 전자 빔 또는 접착식 결합 분말 사후 소결을 사용하여 금속 분말을 국소적으로 융합할 수 있는 비교적 새로운 기술입니다.
금속 분말 제조의 주요 경로는 다음과 같습니다.
- 고체 금속의 파쇄
- 용액에서 소금 침전
- 금속 카르보닐의 열 분해(카르보닐 공정)
- 산화 금속의 고체 상태 감소
- 전착
- 용융 금속의 미립화
선택하는 분말 제조 경로는 생산하는 금속 또는 합금, 최종 사용 응용, 해당 공정에 필요한 특정 분말 특성에 따라 달라집니다. 예를 들어, 가스 미립화된 금속 분말은 많은 분말 야금 응용 분야에서 사용되지만 필요한 특성을 제공하기 위해 특정 크기의 분율이 필요한 경우가 많습니다.
물질 특성 분석이 중요한 이유는 무엇입니까?
금속 부품이나 정확한 속성의 제품을 지속적으로 생산하려면 알려져 있고 신뢰할 수 있는 특성을 가진 입력 물질이 필요합니다. 금속 분말의 경우 여기에는 적절한 분석 기법을 사용하여 측정해야 하는 화학, 형태 및 미세구조 특성이 포함될 수 있습니다.
금속 분말에서 중요한 특징은 무엇입니까?
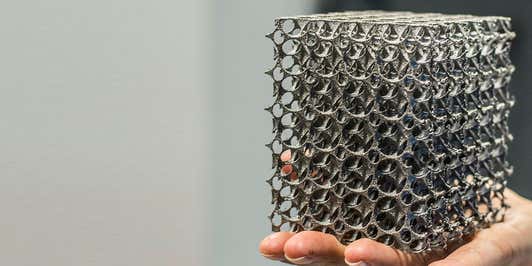
입자 크기와 입자 형상은 분말 흐름, 분말 패킹, 기공률, 반응성, 심지어 건강 및 안전에도 영향을 미치기 때문에 대부분의 금속 분말 공정에서 중요한 특성입니다. 이러한 특성은 분사, 살포, 압축 또는 소결 등 특정 최종 공정에 맞게 최적화되어야 합니다. 지정된 물질의 합금 조성을 준수해야 하며, 침입형 원소의 존재를 제어하기 위해 등급을 주의 깊게 선택해야 하는 분말 야금 및 적층 제조의 경우 화학은 특히 중요합니다.
금속 분말과 조립된 부품의 기계적 및 화학적 특성에 영향을 줄 수 있기 때문에 결정학적 구조 또한 중요한 요소입니다. 특정 응용 분야의 특정 상 조성과 입자 크기 및 질감을 갖도록 분말을 엔지니어링해야 하는 경우도 많습니다.
또한 분산된 고분자/왁스 매트릭스나 인쇄 잉크로 된 금속 분말을 공급 원료 물질로 사용하는 금속 사출 성형과 같은 공정에서는 유변학적 특성이 중요합니다. 이러한 특성은 입자 크기, 모양, 입자 농도 등의 입자 특성에 영향을 받습니다.
Malvern Panalytical은 어떤 금속 분말 분석 솔루션을 제공합니까?
당사의 주요 입자 특성 분석 솔루션은 뛰어난 자동화를 자랑하는 벤치톱 기기인 Mastersizer과 Morphologi 4입니다, Mastersizer 3000은 레이저 회절을 사용하여 입자 크기 분포를 측정하며, 이 기법은 Insitec을 사용하여 온라인으로 적용할 수도 있습니다. Morphologi 4는 디지털 카메라를 사용하여 분산된 입자의 고품질 2D 이미지를 캡처하고 입자별 크기 및 형상 정보를 캡처하는 자동 이미징 시스템입니다. 금속 나노입자와 분산의 경우 Zetasizer 제품군이 보다 적절한 솔루션이 될 수 있습니다. 이 제품은 동적 광산란 및 전기 영동 광산란을 사용하여 각각 입자 크기와 제타 전위를 측정합니다.
원소 분석을 위해 X선 형광(XRF)을 사용합니다. 이 X선 형광(XRF)은 응용 분야의 요구 사항에 따라 스탠드형(Zetium)과 벤치톱(Epsilon) 옵션으로 제공됩니다. 또한 Claisse 포트폴리오를 통해 XRF, ICP, AA를 위한 몇 가지 샘플 준비 솔루션을 제공합니다. 구조 및 결정학적 연구에 있어 당사의 주요 솔루션은 X선 회절(XRD)로, 플로어 스탠딩(Empyrean) 및 벤치톱(Aeris) 시스템으로도 사용할 수 있습니다.