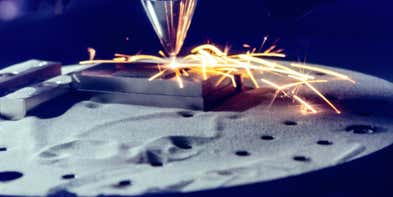
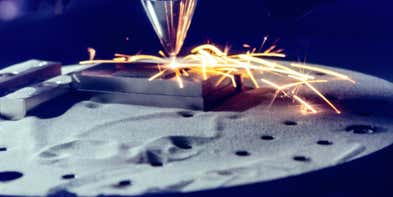
Material characterization solutions for additive manufacturing and 3D printing
Additive manufacturing (AM) – also commonly referred to as 3D Printing – is the process of building three-dimensional structures or components from the ground up, usually layer by layer. It’s an increasingly popular manufacturing process – but to be successful, it requires careful characterization of components’ raw materials, such as metal powders and polymer powders. To meet this need, Malvern Panalytical offers characterization solutions that cover many of the major AM processes and materials used, including:
Please download our brochure to find out more.
The properties of an additively manufactured component are highly dependent on its underlying microstructure. This, in turn, depends on the properties of the raw materials (metals, polymers) and process conditions used. In fixed processes, the biggest source of variation comes from the materials. Inconsistent material properties will result in inconsistent finished component properties. To produce additive manufacturing components of consistent quality, it’s therefore crucial that manufacturers can understand and optimize the characteristics. of their metal powders, polymer powders, or other materials like ceramics and polymer resins.
This depends on the additive manufacturing process being used and the type of materials employed. For example, in metal powder bed processes, such as binder jetting and powder bed fusion, particle size and particle shape are critical because they affect powder flow and packing. Chemical analysis is also very important in these processes – especially for metal powders since the powder needs to comply with the alloy composition of the material specified, which can affect the properties of the finished part.
Crystallographic structure is another important characteristic for metals since the rapid heating-cooling cycles used in certain AM processes can induce phase changes and generate residual stresses, which can then affect mechanical properties such as fatigue life. Finally, for polymer materials, which are used in several additive manufacturing processes, the polymeric structure (branching, crystallinity) can affect both liquid and solid properties, including viscosity, modulus, and thermal properties.
To support additive manufacturers with material characterization, we offer several analytical tools. For particle size and shape analysis, we offer the Mastersizer 3000 and Morphologi 4 – benchtop instruments with a high level of automation. The Mastersizer 3000 uses laser diffraction to measure particle size distribution. This technique can also be carried out online using our Insitec instrument. For particle shape analysis, the Morphologi 4 automated imaging system uses a digital camera to capture high-quality 2D images of dispersed particles, and provides particle-specific size and shape information.
For elemental analysis, we offer X-ray fluorescence (XRF) solutions, which are available in floor-standing (Zetium) and benchtop (Epsilon) variants, depending on application requirements. And, to support with structural and crystallographic analysis, X-ray diffraction (XRD) is our principal solution, which we also offer in both floor-standing (Empyrean) and compact (Aeris) systems. Finally, for determining the molecular weight and structure of polymeric materials, the Omnisec is our main solution, using gel permeation chromatography.