Around the world, batteries are at the heart of revolutionary innovations – whether that’s in smart mobile devices, pollution-free electric cars, intelligent power management solutions, or mass energy storage systems to complement wind and solar power. So it’s vital that they perform as effectively as possible – and that battery researchers and developers can keep developing solutions to improve this performance even further.
Whether you’re associated with battery research or battery development, our battery material analysis solutions can help you achieve high performance faster and more easily. From Li-ion batteries to emerging technologies such as Na-ion, Li-sulphur, Zn-air, or graphene-based modifications, they’ll help you optimize your battery materials to achieve the highest quality. Our solutions can also be used for graphene supercapacitors, which can supplement batteries in applications that need high power for a short time.
By optimizing factors such as electrode material and slurry with, you can achieve the highest battery performance – and help enable the innovations that are building a more sustainable, more connected world.
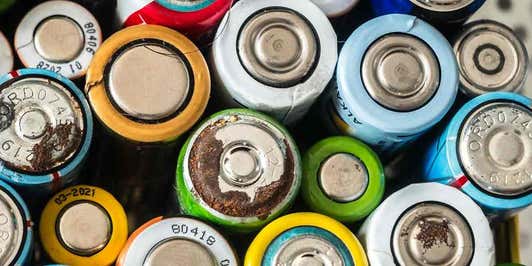
Lithium-ion battery recycling
How can I ensure the quality of my electrode materials?
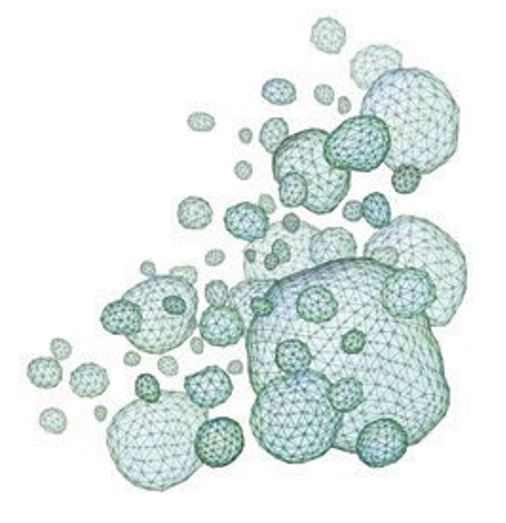
Electrode material quality is influenced by several factors, all of which our solutions can help with:
Particle size : Electrode material particle size plays an important role in battery performance. Particle size variation must usually be regularly measured and optimized to maintain consistent battery performance – ideally, over the course of the production process.
Based on laser diffraction, our Mastersizer offers the easiest, most accurate way of measuring cathode and anode material particle sizes. And, for industrial process environments, it can be replaced by our Insitec on-line particle size analyzer to provide real-time data for process control.
Particle shape : Particle shape in battery electrode materials holds the key to unlocking any given material’s potential to produce the best-performing battery. Specifically, particle shape affects slurry rheology, as well as the packing density, porosity, and uniformity of electrode coatings.
Accordingly, to achieve the highest levels of battery performance, manufacturers must be able to analyze and optimize particle morphology. Our Morphologi 4 optical imaging tool can analyze the size and shape of statistically relevant ensembles of particles in just a few minutes, to empower you with all the critical information you need to optimize your battery slurry.

Crystalline Phase : Crystalline phase defines the structure of materials at atomic scale – the scale at which ionic or electronic transport happens or is hindered. Crystalline phase composition defines the overall electrode material quality and its suitability for the battery cell manufacturing. X-ray diffraction is the technique of choice when it comes to the analysis of crystalline phases.
Aeris compact X-ray diffractometer, an easy to use instrument with superb data quality, can be used for accurate analysis of:
- Crystalline phase composition and presence of any residual reactants (optimization of calcination process)
- Crystallite size (related to the primary particle size)
- Degree of graphitization in synthetic anode graphite
Chemical composition and impurities: X-ray fluorescence is an alternative technique to ICP to analyze chemical composition and impurities from few ppm up to 100% levels. For major elements at few % levels, XRF provides a simpler and more accurate way of measuring elemental composition than ICP as it does not require any sample dilution or acid digestion. Many leading battery companies use our benchtop E4 XRF or Zetium WDXRF to analyse cathode and pre-cursor materials.
Solutions for electrode quality control
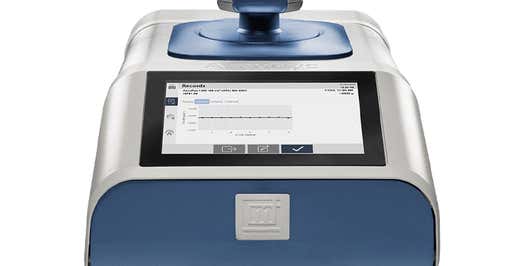
Micromeritics AccuPyc
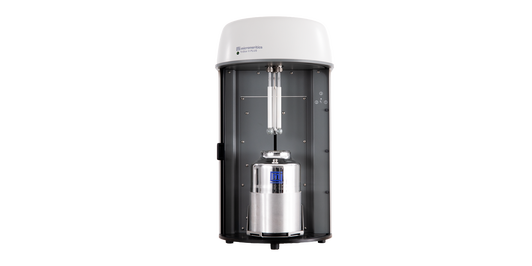
Micromeritics TriStar II Plus
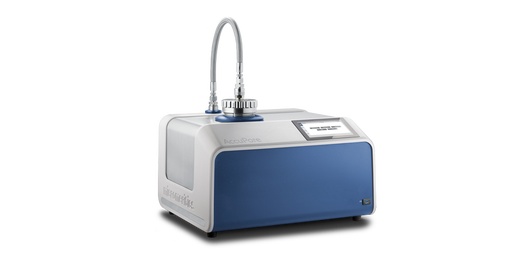
Micromeritics AccuPore
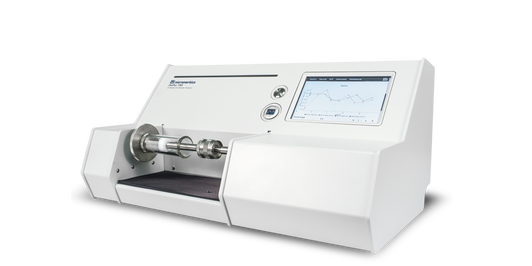
Micromeritics GeoPyc
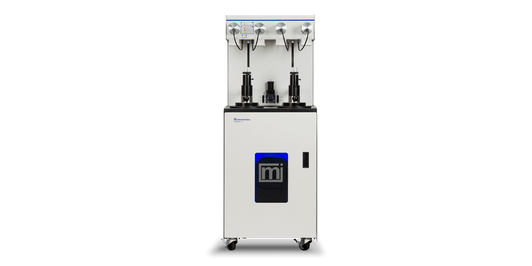
Micromeritics AutoPore V
How can I optimize electrode slurry and ensure its stability?
Battery slurry has many components – electrode material, carbon or graphene, polymer binder, and solvent – and their interconnected structure plays an important role in the quality of electrode coatings. While particle size and shape both influence coatings’ packing density and porosity, another important factor to consider is zeta potential. The zeta potential of electrode particles in slurry determines whether the particles are prone to aggregation.
Particles with high zeta potential will repel to form a stable dispersion, whereas low zeta potential will cause particle aggregation. This, in turn, leads to non-uniformity in the electrode coating, resulting in diminished battery performance. Zeta potential also affects the wettability of the metal surface. Our
Zetasizer
can help you optimize zeta potential to improve the quality of your electrode coatings – with excellent accuracy, repeatability, and consistency.
How can I enhance battery performance with graphene?
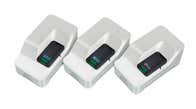
Zetasizer range
Analyze the zeta potential of graphene
In the battery industry, graphene is known to enhance the performance of both cathode and anode materials by providing an electronic conduction network. When modifying cathode material with graphene, zeta potential can significantly affect how the graphene and lithium cathode particles interact.
To help you monitor this, in order to make your graphene enhancement as effective as possible, our Zetasizer can analyze the zeta potential of both graphene and cathode particles. It can also help you adjust Ph values for optimum interaction – so that using graphene will add maximum value to your battery’s performance.
Featured content
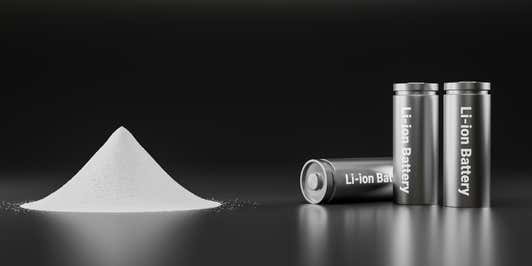
Graphitization degree and orientation index in graphite anode materials
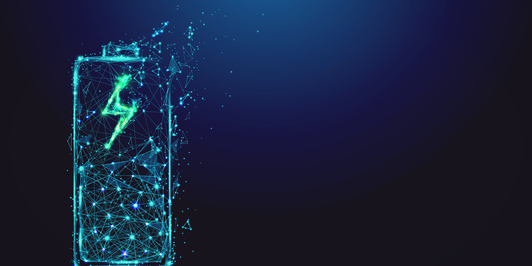
Battery manufacturing: Reliable, adaptable particle sizing using the Mastersizer 3000+
Working with super- and ultra-capacitors?
Graphene or activated-carbon-based supercapacitors complement batteries in applications that need high power for a short time. Supercapacitors are very similar to batteries in material. Indeed, particle size, morphology, phases and interlayers, rheology, and phase changes associated with charge-discharge cycles play an equally important role for supercapacitors as for batteries. And, fortunately, our innovative solutions can all also be used to analyze and improve the performance of supercapacitors.
Solutions for battery research and quality control
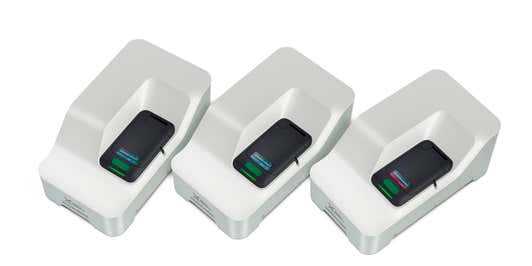
Zetasizer range
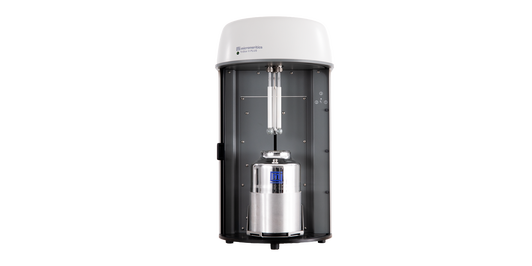
Micromeritics TriStar II Plus
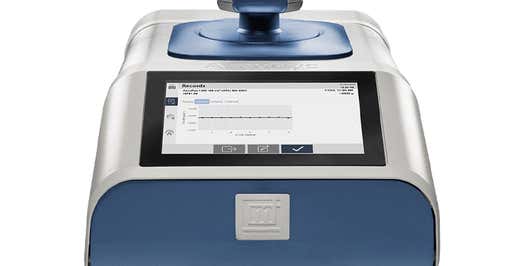
Micromeritics AccuPyc
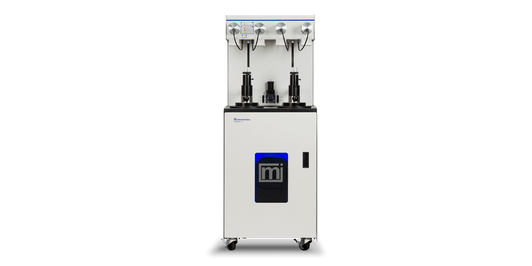
Micromeritics AutoPore V
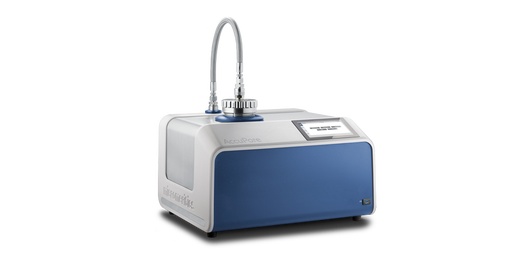
Micromeritics AccuPore
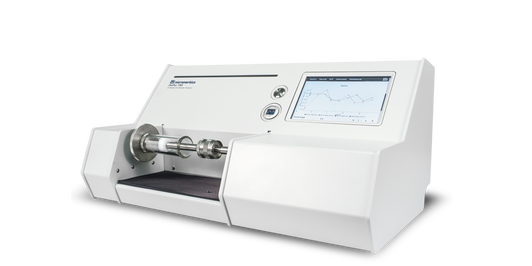