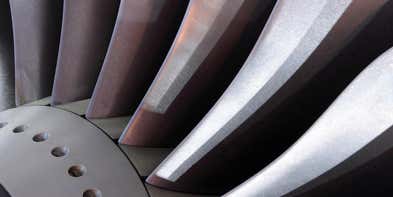
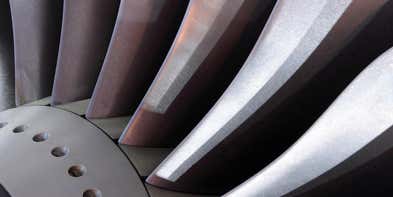
Material characterization solutions for metal powders and powder metallurgy
Powder metallurgy is an umbrella term covering several processes used for manufacturing metallic components from metal powders. The main processes include:
To achieve consistently high quality in these metallic components, the properties of the metal powders must be carefully analyzed and characterized to ensure good powder flow, packing, and friction, and the best metallic composition. Malvern Panalytical offers several material characterization solutions for these processes.
Please download our brochure to find out more.
Particle size and particle shape are critical parameters in powder metallurgy processes, because they affect important properties such as powder flow, powder packing, and interparticle friction. These properties must be optimized to achieve the required strength and density in the green body and sintered components. Chemical composition is also very important because the metal powder needs to comply with the alloy composition of the material specified, which can affect the properties of the finished part.
Crystallographic structure also affects the mechanical properties of both the metal powder and the final component. For this reason, powder production and powder metal parts manufacturing processes need to be engineered to produce materials with the right phase composition, grain size, and texture for the required application – all while minimizing residual stresses .
Finally, for processes such as metal injection molding, where the feedstock material is a dispersion of powder in a polymer/wax matrix, the rheological properties of the feedstock become critical. These properties are influenced by particle characteristics including particle size, shape, and concentration, as well as binder properties such as molecular weight and molecular structure. Manufacturers must therefore be able to control these characteristics.
To support AM manufacturers with material characterization in powder metallurgy processes, we offer several analytical tools. For particle characterization, our main solutions are the Mastersizer 3000 and Morphologi 4 – benchtop instruments with a high level of automation. The Mastersizer 3000 uses laser diffraction to measure particle size distribution. This technique can also be employed online using our Insitec instrument. For particle shape analysis, the Morphologi 4 automated imaging system uses a digital camera to capture high-quality 2D images of dispersed particles, and provides particle-specific size and shape information.
For elemental analysis, we offer X-ray fluorescence (XRF) solutions, which are available in floor-standing (Zetium) and benchtop (Epsilon) variants, depending on application requirements. And, to support structural and crystallographic analysis, X-ray diffraction (XRD) is our principal solution, which we also offer in both floor-standing (Empyrean) and compact (Aeris) systems. Finally, for determining the molecular weight and structure of polymeric materials, the Omnisec is our main solution, using gel permeation chromatography.