Single-crystal substrate materials with carefully controlled composition and crystal orientation are at the heart of semiconductor manufacturing. The thin film structures created on these substrates are then shaped by sophisticated processes into intricate devices on a wafer. Typical materials involved in advanced thin film devices are semiconductors, metal alloys, dielectrics, oxides, and polymers. This mandates accurate monitoring and control of substrate, thin film and device manufacturing using multiple metrology techniques. Equally important is the fine control over the process materials, for example CMP slurries and plating solutions.
Single crystal substrate manufacturing involves seeding, crystal growth, grinding, cutting, polishing and final control. Throughout all these steps, quick and precise crystal orientation control is critically important to ensure cost efficient production of high-quality substrates.
These substrates are the foundation for the thin film-based devices, which are manufactured using a complex multistep fabrication process. X-ray fluorescence (XRF) or X-ray diffraction (XRD) are an integral part of any such manufacturing process to monitor and control critical thin film parameters at every step.
In a different process flow, electronic displays employ various technologies such as liquid crystals, pigment dispersions, quantum dots, and OLEDs. In most of these, the particle size and shape play an important role and count on our particle characterization range for reliable characterization. For OLEDs, we provide strict control over the polymer characteristics such as size and molecular weight which is paramount to the display quality.
Analytical solutions for the electronics industry
Malvern Panalytical is closely associated with the electronics industry with a wide range of solutions across the entire value chain:
- XRF (2830 ZT) delivers thickness and composition information for a wide range of thin films, with contamination and dopant levels and surface uniformity on wafers up to 300mm in size.
- XRD (X'Pert3 MRD and X'Pert3 MRD XL) provides absolute, calibration-free, and accurate information on crystal growth, giving material composition, film thickness, grading profile, and phase and crystal quality.
- Laser diffraction (Mastersizer) measures particle size distribution in powder and slurry dispersions, e.g. CMP slurry and electronic display materials.
- Crystal orientation (Crystal Orientation Range) fast and accurate orientation for boule, ingot, puck and wafer applications
- Imaging (Morphologi 4) analyzes particle shape and morphology using automated imaging.
- Zeta potential (Zetasizer Range) determines the stability of slurries used in the electronics industry through the measurement of zeta potential. It also measures particle size in nano-particle suspensions.
- GPC/SEC (OMNISEC) analyses size, molecular weight, intrinsic viscosity, branching, and other parameters for polymers used in the electronics industry.
- XRF (Epsilon 4): A chemical composition analysis of raw materials and finished products and RoHS/WEEE analysis of electronic components.
- XRD (Aeris): A crystalline phase analysis of raw materials and finished products in electronics industry.
Our solutions
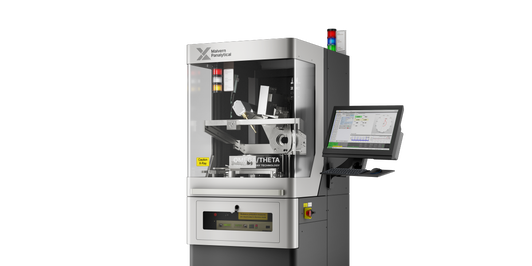
Crystal orientation range
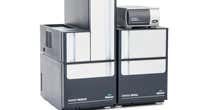