To produce high-quality aluminum at minimal cost, you need efficient processes, with the lowest possible energy use and consistent raw material streams. Optimized processes and materials can also help you meet environmental goals. In order to predict and optimize your material’s behavior, you need to monitor it continuously at all process stages – and respond quickly to the results.
With Malvern Panalytical’s industrial solutions, you can analyze the mineralogical, elemental and particle size composition of bauxite, alumina, and aluminum within minutes for truly future-proof operations.
Your benefits:
- Efficient processes
- Improved environmental effect
- Tailored solutions
Bauxite mining
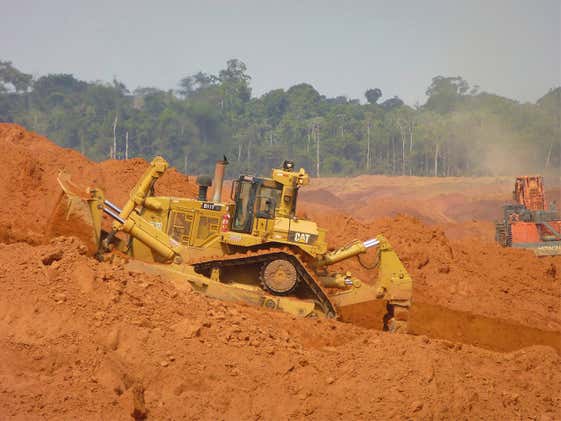
Bauxite is the world’s main source of aluminum, and bauxite ore is mined in open pits before being sorted into grades. The ore is then chemically digested to separate the valuable aluminum oxide, called alumina, from the waste material, which is known as red mud. Once purified, aluminum metal is extracted from the alumina in electrolytic baths. This process looks quite similar around the world, with large-scale bauxite production taking place in many countries. Some of the largest producers include Brazil, Australia, Guinea, Jamaica, China, and Russia.
Not all ores are created equal – bauxite is found in the three main phases of gibbsite, boehmite, and diaspor. Some need higher temperatures during the Bayer digestion process than others, and most manufacturers prioritize gibbsite as it needs the lowest temperatures and therefore consumes the least energy. To sort and grade these different ores, accurate analysis is key.
Any complex and multi-step process requires careful control, and the processing of bauxite is no different. At the mine, a CNA cross-belt analyzer can make grading ores efficient, leading to a more organized stockpile and fewer resources wasted downstream.
Crystalline phase plays a key role in the processing of ores, usually measured on an instrument like the Aeris through X-ray diffraction. X-ray fluorescence is used to characterize elemental composition, and our popular Zetium range comes in a specialized Zetium Metals edition for industry use. Finally, understanding particle size is crucial for the alumina stage, with the Mastersizer a standard solution for laser diffraction.
Alumina
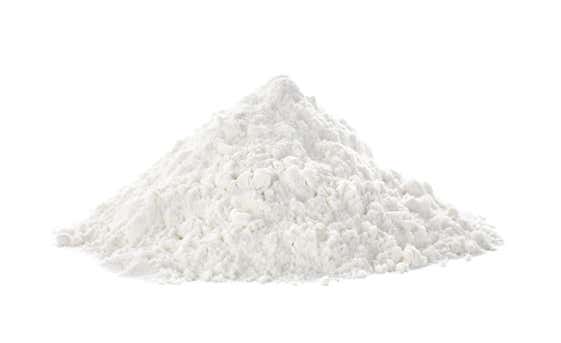
Alumina (Al2O3) is an intermediate raw material generated during the production of aluminum from bauxite ore. Processing parameters such as particle size, Al2O3 polymorphs, or impurities have a direct impact on the use of energy and chemicals during refining and smelting and therefore affect both the efficiency and profitability of the process.
Particle size directly affects the rate of alumina dissolution in the electrolytic baths in the smelter. Furthermore, fines present an issue for both health and safety and product transport. On-line particle-size analysis during the production of alumina has increased throughput by 50%, and achieved payback within 12 months by avoiding the need to reprocess ‘out of spec’ material.
Knowledge of the different Al2O3 modifications is vital in predicting and optimizing its behavior during the smelting process. γ-Al2O3 is the desired polymorph for electrolysis, as it dissolves more easily during the smelting process than α-Al2O3. For this reason, the ratio of the different polymorphs of alumina must be monitored with X-ray diffraction (XRD).
The drive for sustainable metal manufacturing and increased ESG requirements make fast and accurate impurity monitoring mandatory in liquors and red mud. Our X-ray fluorescence solutions allow elemental analysis in real-time, during the process and in the laboratory. XRD instruments can monitor the phase composition of red mud, which ensures compliance with safety and environmental standards.
Aluminia measurement solutions
Aluminum smelting
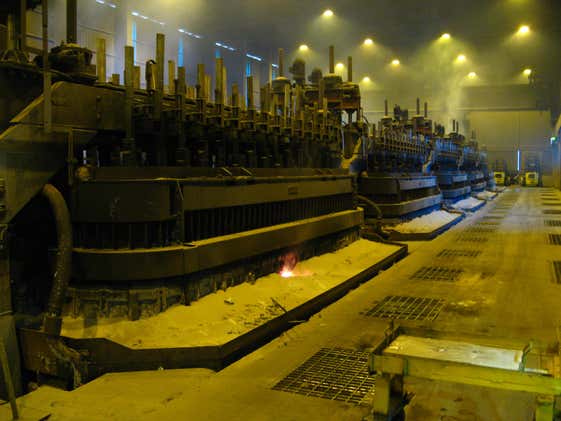
Production of aluminum from purified alumina by electrolysis (the Hall-Héroult process) requires an immense amount of electrical energy. Continuous monitoring of the bath composition is of paramount importance in determining, adjusting, and maintaining optimal conditions, which result in significant cost and energy savings when successfully carried out.
X-ray diffraction (XRD)
makes it possible to monitor electrolytic bath composition, as well as quickly and accurately predict the relevant process parameters of different types of electrolytic baths (with the addition of Ca, Mg, Li, and K). The method calculates bath ratio along with excess AlF
3
and CaF
2
, as well as free alumina content and liquidus temperature.
The respective lifetime of carbon anodes, that are required and consumed during aluminium smelting, are mainly controlled by the average crystallite size (Lc) of the graphite platelets, as well as particle size and contaminations. XRD is a standard method (ASTM D5178) for the determination of crystallite size, and is implemented in Malvern Panalytical’s solution for electrolytic bath analysis.
To ensure frequent and safe analysis, Malvern Panalytical offers completely automated laboratory solutions, including sample preparation tailored to the specific needs of each aluminum smelter.
Aluminum processing solutions
Aluminum alloys
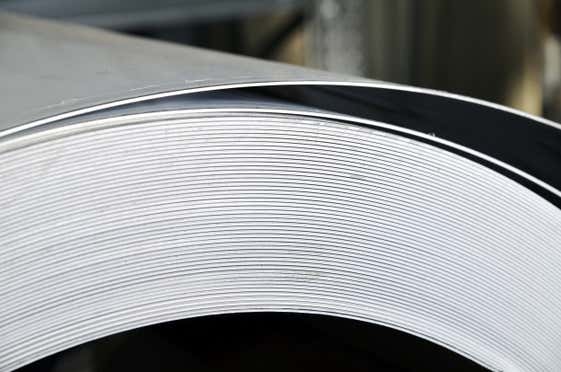
Aluminum metal and its alloys can be found everywhere in our daily life; in cars, cans, smartphones, and airplanes. To guarantee high-quality standards of alloyed or coated aluminum, permanent control of composition and impurities is mandatory for manufacturers – whether the aluminum is produced from primary raw materials or recycled material.
Our high-throughput analytical solutions based on XRF technology allow the monitoring of aluminum metals and alloys and can be automated and adapted to each manufacturing process. XRD can also check metal properties such as stress and texture to avoid out-of-spec metals production.
Recycled aluminum
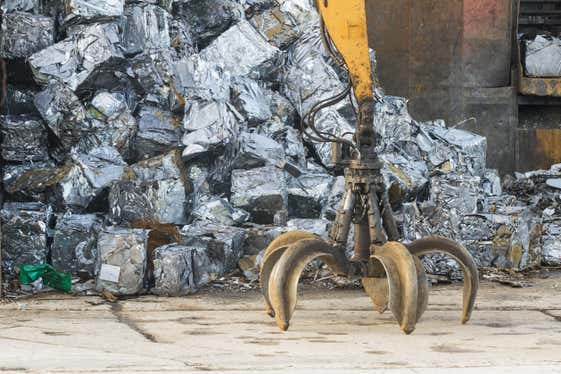
As the metals industry moves toward more sustainable processes, recycling materials is becoming an increasingly important strategy for reducing environmental impact. Aside from preventing waste, recycled materials usually require less processing and therefore less energy.
Recycled aluminum is already growing in popularity as a commodity with a lower carbon footprint. However, working with recycled materials makes quality control and accurate analysis very important. With no control over the production process, manufacturers need an in-depth understanding of the material’s properties to ensure safety and reliable performance.
When accuracy is key, a specialized solution is needed. Malvern Panalytical’s Zetium range of X-ray fluorescence analyzers includes a Metals edition, designed for the specific needs of the metals industry. The Zetium is perfectly suited to demanding quality control applications, and enables manufacturers to get the most out of recycled materials – lowering environmental impact and maximizing profitability.
Aluminum analysis instrumentation
Related resources
Optimising aluminium production with on-line particle size analysis
Characterization of metals using X-ray diffraction (XRD) - Residual stress and texture analysis
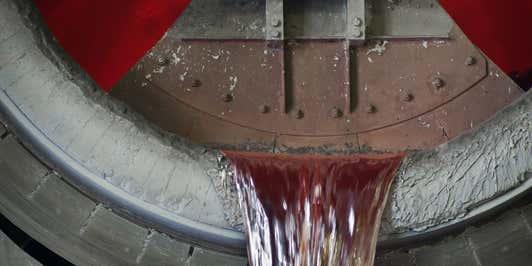