Cathode active materials (CAMs) are essential components in lithium-ion batteries (LIBs), playing a key role in determining energy density, lifespan, and safety. These materials are used in the positive electrode of batteries and are crucial for applications like electric vehicles, electronics, and energy storage.
The performance of CAMs is influenced by factors such as voltage, capacity, cycle life, thermal stability/safety, and cost. Research and development in CAMs focus on enhancing these properties through methods such as element doping, novel crystal structure development, and exploring alternative materials like solid-state cathodes. The aim is to improve battery performance, reduce costs, and enhance safety, which are all critical for advancing the future of energy storage technology.
Chemical composition, crystalline quality and particle size and shape are the key parameters governing the quality and process efficiency of the cathode materials.
Solutions for cathode active materials
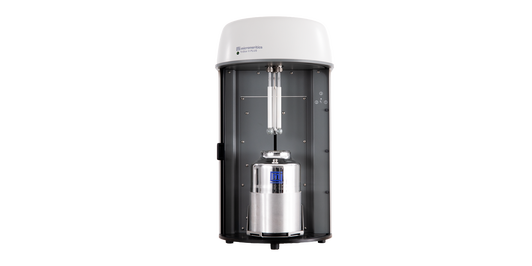
Micromeritics TriStar II Plus
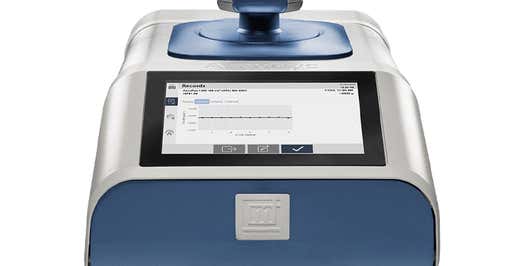
Micromeritics AccuPyc
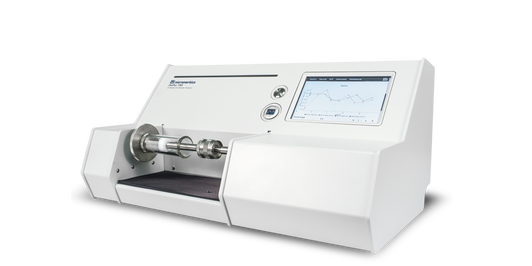
Micromeritics GeoPyc
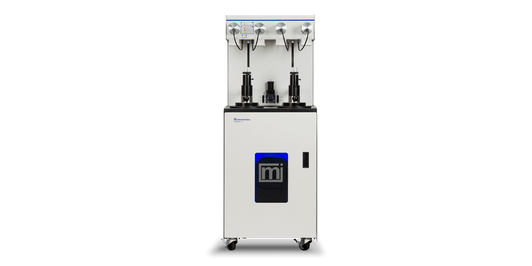
Micromeritics AutoPore V
Types of CAMs
- Lithium Cobalt Oxide (LiCoO₂): High energy density, but costly and less safe.
- Lithium Iron Phosphate (LiFePO₄): Excellent safety and long cycle life, though with lower energy density, making it ideal for electric vehicles.
- Lithium Nickel Manganese Cobalt Oxide (NMC): Balanced properties of high energy density, stability, and cost-effectiveness, widely used in electric vehicles.
- Lithium Nickel Cobalt Aluminum Oxide (NCA): Offers higher energy density, suitable for high-performance applications like electric vehicles.
- Lithium Manganese Oxide (LiMn₂O₄): Safe and powerful but with lower energy density and shorter lifespan, used in niche applications.
CAM synthesis and processing
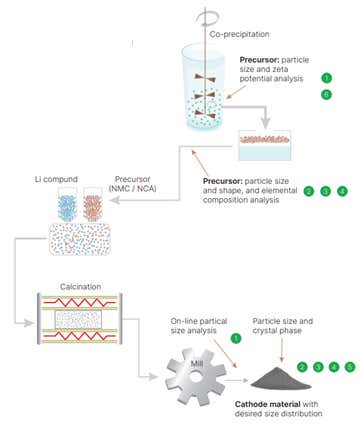
The most common method for synthesizing cathode materials is co-precipitation of the metal precursor (usually metal oxides, carbonates, or hydroxides) followed by solid-state synthesis, where the metal precursor is mixed and ground together with the Li precursor, then calcined at high temperatures (typically 800-1000°C) in a controlled atmosphere to form the desired crystalline phase. The calcined material is then ground to the desired particle size. The process is schematically shown in the figure to the right.
Cathode materials of current interest, such as NCA and NMC, are produced via co-precipitation of a transition metal hydroxide precursor, followed by calcination (lithiation and oxidation) with a lithium compound.
Our morphological, structural and elemental insights can help to:
- Optimize process parameters
- Ensure consistent quality
- Reduce production costs
To monitor and control the synthesis parameters in real-time and to optimize the quality of synthesized CAMs, we offer a range of analytical solutions for particle size and shape, elemental composition and crystalline quality and defects. What’s more, our solutions also help you to ensure that the used precursor materials also have the desired properties.
How do I characterize my cathode active materials?
Cathode materials quality and throughput can be optimized by measuring and controlling the following parameters:
- Particle size and shape
- Crystal phase and crystal defects (cation mixing, crystallite size, graphitization degree)
- Elemental composition and impurities (Ni, Co, Mn)
Particle size and shape
Whether you produce your own active materials or buy them from your suppliers, particle size and particle shape are the defining parameters for not only battery performance, but also an uninterrupted high-yield production process.
Particle size and shape govern the production yield of precursor materials, the rheology of the electrode slurry, packing density/porosity of the electrode coating, and ultimately the performance of the battery.
The best way to measure these is with a combination of laser diffraction and automated optical imaging.
Mastersizer range
The smartest way to measure particle size
Mastersizer 3000+
Delivering the data you need, for the outcomes you can trust
The Mastersizer range of laser diffraction particle size analyzers set the standard for delivering rapid, accurate particle size distributions. With a wide size range and best-in-class accuracy, Mastersizer 3000+ is the tool you need for CAM particle sizing. And when you get unexpected results on your sample, you have the data guidance tools for further investigation.
Add in flexibility, ease of use, and Hydro Insight accessory for dynamic imaging, the Mastersizer truly is the top choice for particle sizing and beyond.
Explore our particle size and shape solutions
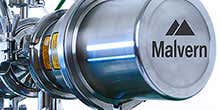
Insitec range
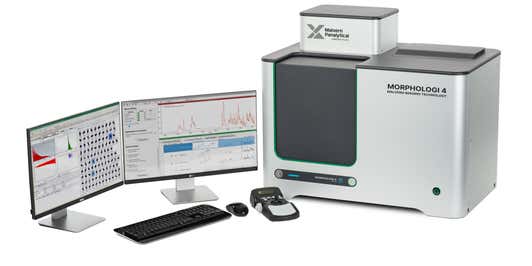
Morphologi 4-ID
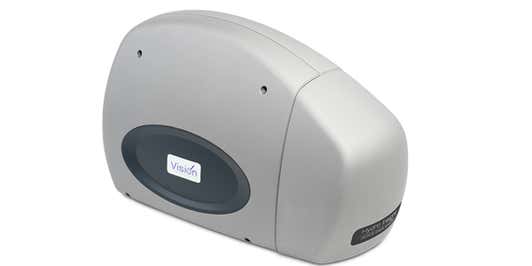
Hydro Insight
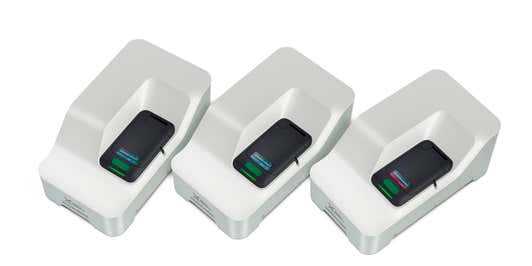
Zetasizer range
Crystal phase
The quality of the crystal phase is another critical parameter that governs the performance of battery materials like specific energy and discharge rate or capacity.
For Cathode active materials, important parameters of concern are cation mixing and crystallite size. Crystallite size can also give an idea about the particle size of nano-crystalline active materials like silicon-based anode.
If you are working on single-crystal cathode materials, then measurement of crystallite size becomes even more critical.
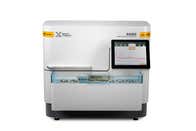
Aeris
The future is compact
Aeris
The future is compact
Aeris XRD can analyze anode and cathode materials in just a few minutes to provide quality parameters like crystallite size, cation mixing, graphitization degree and orientation index.
This is a compact plug-and-play XRD system, built with industrial robustness and safety. Moreover, it can be easily integrated to the process with belt or robot automation.
Elemental composition
For cathode active materials and their precursors, having correct elemental composition is equally as important. Also important are the dopant and impurity concentrations both for the cathode and anode materials.
ICP is a common way of measuring elemental composition, however, it is expensive, time-consuming and involves hazardous chemicals. X-ray fluorescence (XRF) can analyze most of these materials with relative ease.
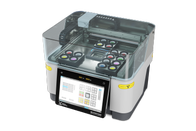
Revontium
Compact brilliance, powerful analysis, endless possibilities
Revontium
Compact brilliance, powerful analysis, endless possibilities
Revontium is a compact X-ray fluorescence (XRF) analyzer that delivers high-quality elemental analysis in a compact, tabletop format. It bridges the performance of floor-standing XRF and the versatility of table-top instruments.
Compact XRF offers a smaller physical and environmental footprint. Its cost of ownership can be more than 25% lower due to reduced need for consumables, extensive sample preparation, and maintenance.
📚 Read the blog: How XRF calibration helps improve NMC battery production
Explore our elemental composition solutions
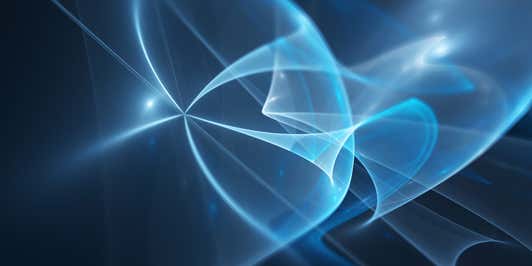
WROXI - Certified Reference Materials
Further reading
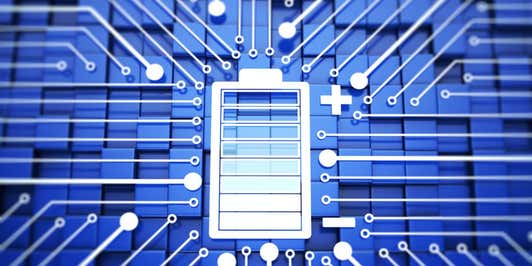
What XRD configuration shall one use to analyze battery cathode materials?
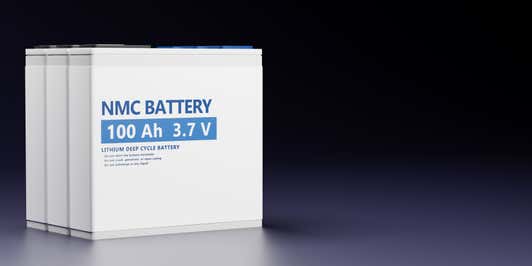