Over the past 30 years, the use of commercial and industrial printing has changed substantially. In particular, the maturation of inkjet technology has revolutionized the printing industry - from office printers through to industrial coding and marking systems, and now ceramic, corrugated cardboard, and 3D printing applications. Similarly, the demand for toner use has continued to rise as the cost of photocopiers and laser printers has decreased and they become more prevalent in offices and homes.
To continue to meet the growing demand for high-quality inks, coatings, and toners, manufacturers must carefully optimize their properties. Malvern Panalytical offers several analytical tools to support this.
Why is characterization important?
To achieve the best performance in their final products, manufacturers of inks and coatings must optimize the properties of their raw materials. Inks, for instance, are complex dispersions or emulsions made of dyes, pigments, and other components suspended within a continuous phase. The properties of these components affect multiple aspects of ink performance. For example, the particle size of suspended pigments determines the hue, gloss, and weatherability of the finished coating. Similarly, the polymeric continuous phase affects the formulation’s rheological properties and film-forming characteristics, which are key for jetting, spreading, and film robustness.
In contrast to inks, toners are powder formulations, electrically charged to adhere to oppositely charged drums, plates, or pieces of paper, and to melt at elevated temperatures when exposed to a laser. Toner particles contain a mixture of pigment, polymer, and charge control agent (CCA). In the case of magnetic toners, they may also contain ferrites (FexOy). The optimum size for these particles is 3-10μm, and a spherical or quasi-spherical shape enables improved color quality and efficiency.
As such, characterization of ink and coating materials is important across the whole ink and toner supply chain – whether that’s developing, manufacturing, and qualifying raw materials for use in a formulation, or formulating those components to create a robust product with the best performance characteristics and quality attributes.
What characterization solutions does Malvern Panalytical offer?
Particle size
Particle size analysis is critical to the performance of any product containing particulate material – whether in a dispersion, suspension, powder, or spray.
Laser diffraction is the most popular tool for this and our Mastersizer is considered the industry standard for a range of applications, with dry and wet dispersion capabilities and a wide dynamic range. It can be used for monitoring powder milling or precipitation, checking particle size distribution in final products, or developing and researching new products.
We also offer Spraytec, a laser diffraction product specifically designed for spray analysis, and our online Insitec analyzer, which can be integrated into processes for real-time particle sizing and automated control. For accurate analysis of nanoparticle dispersions (< 1 µm), the Zetasizer Advance range may be more appropriate. This uses dynamic light scattering to measure dispersed particles to below 1 nm in diameter.
Dispersion stability
As well as measuring particle size distribution, the Zetasizer Advance Range can also measure the zeta potential of a dispersion. Besides influencing ink stability, zeta potential can be used to probe interactions within a formulation, or measured on a surface to investigate substrate interactions.
Particle shape
We can also support you with analyzing particle shape. Specifically, with our Morphologi 4 automated imaging system, you can determine the size and shape of spherical and irregular particles by analyzing tens of thousands in a sample and classifying them accordingly. What’s more, our Morphologi 4-ID combines automated imaging with Raman spectroscopy to provide particle-specific chemical information.
Elemental analysis
Our primary tool for elemental analysis is X-ray fluorescence (XRF) – used for the analysis and manufacturing of pigments and toners. XRF can also be used to determine the concentration of a given element or compound, such as titanium dioxide, or to detect trace levels of toxic elements, such as in food packaging. We offer both floor-standing XRF spectrometers like the Zetium, and benchtop XRF systems like the Epsilon 4.
Polymer analysis
Inks and toners typically have a polymeric component which functions as a film-former or binder. The macromolecular structure of that polymer directly affects the ink or toner’s film-forming properties, melt characteristics, and rheological behavior. Polymer analysis can help ink or toner manufacturers optimize these properties.
To determine the molecular weight of macromolecules, gel permeation chromatography (GPC) is a popular tool. When combined with advanced detection, it can also provide additional information related to molecular size and structure, such as branching. Combining GPC and Advanced Detection, our OMNISEC GPC system can be used to analyze low-molecular-weight materials such as oligomers, photo-curable resins, and epoxy resins – as well as the higher-molecular-weight polymers used in toners.
Bulk and surface microstructure
Many pigments used in coatings are multi-phase crystalline or semi-crystalline materials. When manufacturing these materials, it’s important that powders have the correct structure and phase. For example, titanium dioxide (TiO2) can have different properties depending on the relative amounts of rutile and anatase and their crystallite sizes.
To determine the key microstructural characteristics of metal and inorganic materials commonly used in paints, such as phase composition and crystallite size, X-ray diffraction (XRD) systems such as our Aeris and Empyrean are ideal. What’s more, the Empyrean – our multipurpose diffractometer – can also be used to study both the structure and residual stresses of thin films. This makes it ideal for examining the properties of the coating itself.
Our solutions
Mastersizer range
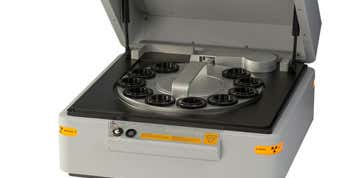
Epsilon 4
Featured content
Using the Zetasizer to optimize formulation stability
The measurement of ink jet inks using laser diffraction particle size analysis
Detecting over-sized particles in ink-jet inks using laser diffraction particle size analysis
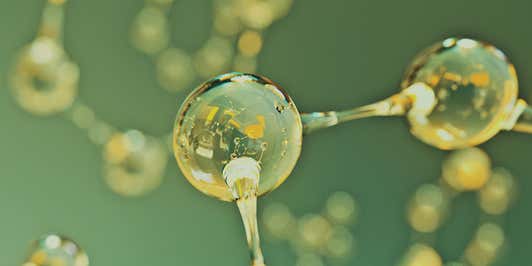