Consistent production of safe, effective medicines that meet their approved specifications involves the establishment of and continued adherence to a set of tightly-defined drug product manufacturing and quality criteria.
The chemistry, manufacturing and controls (CMC) requirements rigorously detailed for every pharmaceutical product encompass the specific manufacturing process, product characteristics and associated product testing which must be applied. Within this, the increasing adoption of QbD approaches ensures early determination of a product’s critical quality attributes (CQAs), identification of the critical material attributes (CMAs) and critical process parameters (CPPs) that affect them, followed by implementation of a suitable control strategy. Many of the analytical methods developed in the early stages of development will carry right through to manufacturing and pharmaceutical quality control (QC).
Defining and validating analytical methods for routine use to meet the specified testing requirements is integral to successful commercial manufacturing and control. Testing must be reliable and robust, and capable of delivering results that can be trusted - every time. In conforming to pharmaceutical industry quality requirements, analytical systems must safeguard data integrity, an issue of growing concern that is attracting significant regulatory oversight and action.
Malvern Panalytical supports pharmaceutical manufacturing and pharmaceutical quality control processes with a wide range of complementary physicochemical characterization tools, underpinned by the in-depth applications understanding and industry expertise that help you make the secure measurement choices essential to maintaining regulatory compliance.
Support with quality control measurements
QC laboratory data informs some of the most critical decision-making in pharmaceutical manufacturing. Analytical solutions must be deployed to track CMAs in line with CMC documentation and, with a plethora of regulatory guidelines to work towards, workhorse instruments with easy, well-developed methodologies and rigorous data tracking are essential.
Malvern Panalytical has deep expertise in the relevance of different physicochemical analysis tools throughout the pharmaceutical lifecycle. We also understand the relationship of these techniques to, for example, the bioavailability strategies employed, including particle size and polymorph selection.
As a result, our teams can support you at every stage in implementing solutions and developing methods that ensure robustness. Importantly, our analytical solutions offer data integrity and 21 CFR Part 11 compliance, with enhancements in data security that provide confidence in meeting regulatory requirements and ensuring full data traceability.
Analytical solutions for pharmaceutical QC
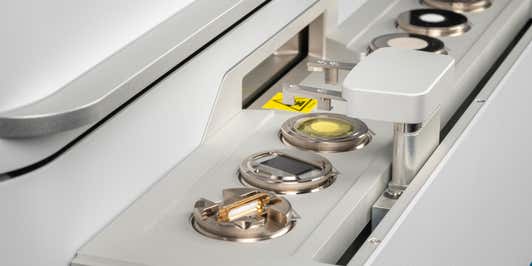
Aeris XRD for pharma
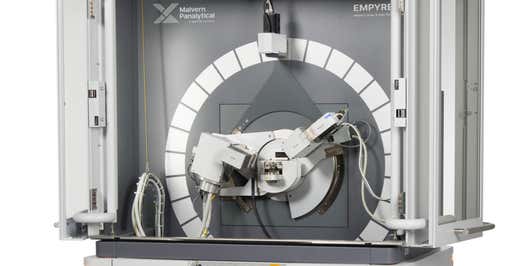
Empyrean
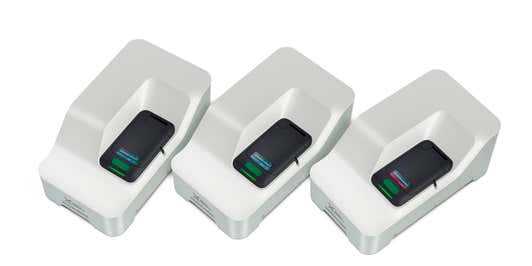
Zetasizer Advance Range
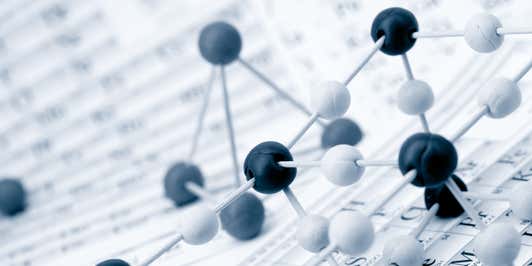
XRF for pharmaceutical development
Particle Size and 21CFR Part 11 - Data Integrity with your Mastersizer 3000
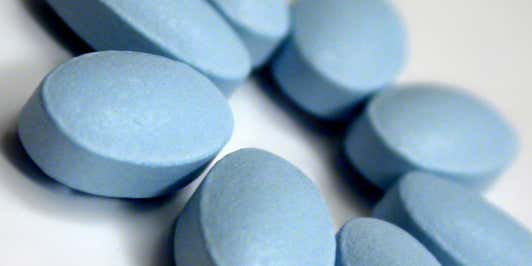
Analytical techniques with a place in the oral solid dosage formulation toolkit
Automation of QC microscope measurements of a pharmaceutical ointment using the Morphologi particle characterisation system
Support with process
While traditional end-product testing provides a measure of whether or not the required quality has been achieved, the application of process analytical technologies (PAT) enables the active maintenance of a product’s specifications within its design space. PAT tools provide the means to understand and monitor CPPs and, as continuous processing gains momentum in pharmaceutical manufacturing, these in- and online analysis tools are essential to its enablement.
Particle size distribution is a critical parameter throughout many pharmaceutical manufacturing processes. Here, the application of fully-automated real-time particle size measurement enables the monitoring and control of processes such as milling and spray drying, from development through to commercial manufacture.
In granulation operations, tracking particle size is important for endpoint detection and process control. Here, inline probes enable particle detection in batch granulation processes, and for real-time monitoring of continuous manufacturing processes.
PAT tools for process optimization and control
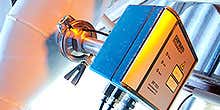
Parsum range
Featured content
New Parsum probe - fit for purpose PAT for granulation particle size monitoring
10 reasons to adopt on-line particle size analysis
The optimization and scale up of high shear granulation: exploring the benefits of real-time particle sizing
Sieve less, see more! In-line particle sizing improves process control
Support with validation
Data integrity associated with analytical techniques has become one of the biggest regulatory concerns in recent years, and one of the most frequent subjects for FDA warning letters. Selection of a 21 CFR Part 11 compliant system, proper instrument qualification and the development of fit-for-purpose methods that are rigorously applied, are all essential.
Validation is a continual and often demanding process. Malvern Panalytical provides extensive support, tailored for users in the pharmaceutical industry, to help make it less onerous. We promote and assist with the correct and appropriate use of an instrument throughout its life, and the lifetime of the pharmaceutical product.
- Extensive instrument lifecycle documentation includes full Installation Qualification (IQ) and Operational Qualification (OQ)
- Help with method development and selection ensures realistic application of the technology to achieve validated methods
- Support with 21 CFR Part 11 compliance ensures that a system is deployed correctly and that methods are being followed properly throughout the entire workflow.
In-depth support is available through Amplify Analytics, a unique partnership between Malvern Panalytical and Concept Life Sciences, which brings together their collective expertise in chemistry and physicochemical analysis. Amplify Analytics offers a range of pharmaceutical contract services, from specific analytical capabilities such as method development and validation, through to provision of fully-integrated drug discovery and development programs.
Featured content
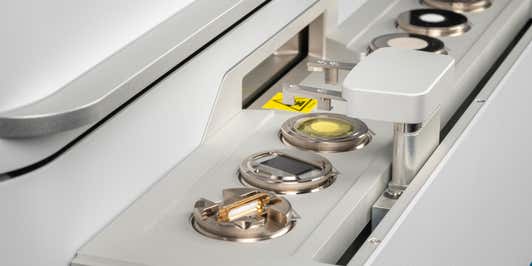
Aeris XRD for pharma
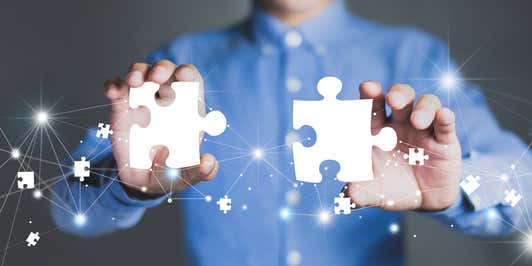
Deploying Expert Analytics: Collaborating to Accelerate Pharmaceutical Development
Drug product manufacture troubleshooting and root cause analysis
Uncovering the root cause of any material or product QC failure is critical in preventing future recurrence. When dealing with a pharmaceutical product, it is essential to look at the final dosage form to understand the process of creating it and establishing where the variance lies.
Morphologically-Directed Raman Spectroscopy (MDRS®) , X-ray powder diffraction (XRPD) and X-ray fluorescence (XRF) spectrometry are powerful technologies that deliver valuable insight for root cause analysis.
MDRS is widely used in development and formulation. It also provides the detailed component-specific morphological descriptions of particulate blends that can help identify anomalies, contaminants and process deviations at the manufacturing stage.
XRPD also has applications in drug discovery, formulation and stability testing. In final product quality control and root cause analysis, it can be used to assess the crystalline structure of the final dosage form and to identify any changes.
XRF enables non-destructive elemental analysis of impurities in active pharmaceutical ingredients, excipients and final drug products.
Systems to speed troubleshooting and root cause analysis
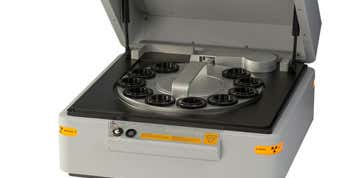